ASG Energy solutions offers modular aluminium compressed air piping for a variety of brands compressed Air systems has what you need at prices that will save you money, modular piping enables elimination of the problem of rust, usually associated with traditional air piping systems. The aluminium oxide in these pipes will eliminate the chances of corrosion in the pipes & ensures the quality of air as per the standards. This technology enables rapid and easy assembly quick connection of the component to the aluminium tubing. Modification to piping can be done without any soldering or threading, to suit your plant requirement. All the pipe and fittings are from leading aluminium piping manufacturer and as per ISO Standard.
ASG Energy Solution provides modular compressor piping and other accessories with highest quality to ensure you get the benefits you deserve. Send us the
Enquiry for more information…
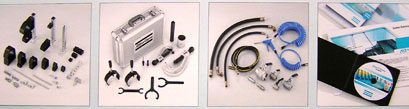
Acting as the vascular system of your manufacturing site, your compressed air sysem plays a vital role in your production processes. Delivering quality air exactly where you need it, at the right pressure and at the lowest possible cost, Atlas Copco’s innovative AIRnet™ compressed air piping system complements your compressed air projects. It consists of high quality elements only and distinguishes itself through flexibility and ease of requirements. Thanks to its wide range of products, AIRnet is a complete solution from source to production.
Features
Reduced energy costs
- AIRnet significantly reduces your operating costs by providing more air flow with less pressure drop thanks to its smooth inner aluminum surface.
- AIRnet’s corrosion-free pipes and fittings minimize the risk of leakage and maintain the pressure drop constant over time, reducing energy waste.
- An integrated drop reduction of 1 bar results in 7% energy savings of your total compressor installed power.
- The compressor is receiver mounted and pre-piped.
Time saving
- AIRnet can be installed easily and quickly by just one person, without requiring any training.
- AIRnet can be installed easily and quickly by just one person, without requiring any training.
- As all components are easily adjustable and reusable, AIRnet evolves right along with your production setting.
- AIRnet is compatible with any existing pipework and equipment.
- To minimize downtime, your installation can be pressurized immediately upon completion.
Benefits
Fully customizable
Fixed to walls or ceilings, AIRnet’s range of fittings lets you custom-build a compressed air system to your specific production needs.
Leakage-free
AIRnet fittings are corrosion-free. They ensure a leakage-free installation and eliminate energy waste.
Maximum flexibility
Quick drops can be added at any time to create extra drop legs. As the connection is made from the side section, the risk of condensate pollutant is eliminated.
Constant air quality
AIRnet delivers constant quality air from point of generation to the various points of use, protecting downstream equipment and manufacturing processes.
Future-minded
As all components are easily adjustable and reusable, AIRnet facilitates future network extensions.
Easy identification
In compliance with most industrial standards, AIRnet pipes are standard painted blue or green for simple network identification.
Low pressure drop
The design with full diameter and inside fin guides eliminates air flow restriction and guarantees the lowest possible pressure drop.
Setting a new standard
A galvanized steel compressed air system has been the industry standard for many years. With AIRnet, Atlas Copco raises the bar in compressed air piping systems, using only highly durable materials like aluminum and polymer.
Higher cost saving potential
AIRnet Pipe
- Smooth surface.
- Constant, low friction factor, resulting in an unrestricted air flow
- Low initial pressure drop. (E.g. In a system with an air demand of 110 l/s, designed as a 400m long ring of o50mm (2″) pipes with P=7 bar, the pressure drop (^P) equals 0.2 bar.)
- Requires lower loading pressure at the compressor and lower power consumption.
- Standard painted blue (compressed air ) or green (inert gases) for easy network identification.
Galvanized pipe
- Rough surface.
- Friction factor is almost double of an aluminum pipe. restricting the air flow. due to corrosion, the friction factor increases over time.
- High initial pressure drop. (E.g. In a system with an air demand of 110 l/s, designed as a 400m long ring of o50mm (2″) pipes with P=7 bar, the pressure drop (^P) equals 0.37 bar.)
- Requires higher loading pressure at the compressor and higher power consumption.
- Pipes need to be painted in the appropriate color, adding to the total cost.
Longer lifetime
AIRnet Pipe
- AIRnet’s aluminum pipes and polymer fittings do not corrode. Their smooth inner surface keeps air clean, now and in the years to come.
- No risk of corrosion when cutting the aluminum.
- Very low risk of leakage, which is not related to corrosion.
Galvanized pipe
- Corrosion protection depends on the quality of the galvanization.
- When the pipe is cut, the galvanization is removed, resulting in a high risk of corrosion.
- The connection poses a high risk of corrosion at low level points where water can stagnate, resulting in a high risk of leakage.
Easier installation
AIRnet PIPE
- Lightweight pipes: a standard 050mm (2″) pipe weights less than 5kg (11ibs).
- Short manual cutting time.
- Fast dedurring of the pipe. Pipes can be simply pushed into the fitting.
- In addition to offering a single assembly method for all fittings, the fitting can be tightened by hand and secured with a spanner.
- Modifying the network is easy and fast: the fittings and pipes can be simply disassembled and refused.
Galvanized pipe
- Heavy pipes: a standard 050mm (2″) pipe weights more than 25 kg (55ibs).
- Very long manual cutting time. Requires an electrical cutter which may generate some metallic dust, polluting the air.
- Threading the pipe requires a certain level of experience to avoid future leakage.
- The galvanized fittings need to be tightened using sealing material. The risk of leakage depends on the quality of the thread.
- Modifying the network is difficult and time-consuming; the pipes have to be cut, changed, threaded and reassembled.
Simple installation
Lightweight yet robust, AIRnet installs easily and fast. Its large range of fittings, sockets, brackets and accessories accommodates any possible network geometry. Quickly adjustable and fully reusable, AIRnet evolves right along with your production setting.
The flexible fit
AIRnet effortlessly adapts to the changing demands of your network. Connection to your applications can be easily and manually dismantled and reassembled to connect to new or modified production process. Quick drop fittings can be added at any time to create extra drop fittings can be added at any time to create extra drop legs. Furthermore, AIRnet is also compatible with any exciting pipe work and equipment.
Reduced installation time
AIRnet has been designed with a unique assembly system, allowing an AIRnet system to be built in one-third the time of a conventional one. Assembling a pipe, from cutting to securing the pipe into the fitting, takes only 2 minutes for fittings of smaller diameters (<o50 mm, 2″), and only 4 minutes for larger fittings. Pipes up to o25 mm (1″) can even be tightened by hand, with instant air tightness. As the system can be pressurized immediately after assembly, you will not waste not waste valuable time.
Immediately airtight
Atlas Copco engineered and manufactured AIRnet to eliminate leakage. While the unique O-ring ensures an airtight fit, the longer push distance facilities achieving perfect alignment for high resistance to vibration. The clinch ring grips the pipe, keeping the fitting firmly in place and securing the installation at maximum working pressure.