If the corrosive sludge is allowed to enter the compressed air system, it will not be long before problems start to appear.Following are some of the most common and most expensive problems:
- Tools and equipment break down more regularly, experience a shorter lifetime and reduced power.
- The end product, or other materials that come into contact with the contaminated air, can suffer spoilage and quality degradation.
- The compressed air pipe work will corrode, leading to leaks and loss of valuable compressed air.
Typical Example
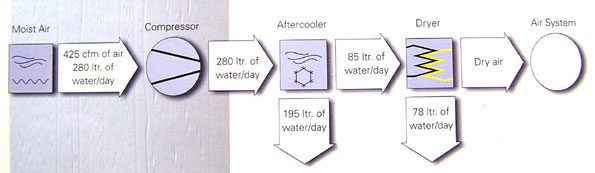
Benefits
Refrigerant Circuit
- Refrigerant Compressor Brings the gaseous refrigerant to a high pressure and a high temperature.
- Condenser Cools the refrigerant slightly so that it changes from gas to liquid as refrigerant is more effective in the liquid state.
- Capillary filter Protects the expansion device from harmful particles.
- Capillary tube Reduces the refrigerant's pressure, thereby lowering its temperature and increasing its cooling capacity; the refrigerant is now almost all liquid, with some residual gas.
- Hot gas bypass Regulates the amount of refrigerant passing through the air-to-refriegerant heat exchanger, ensuring a stable pressure dewpoint, and eliminating the chance of the condensate freezing.
- Max. pressure switch (only for FX 13-15) It is a safety feature that allows to control the Refrigerant Compressor.
- FX control pressure switch (only for FX 13-15) It starts and stops the condenser fan Motor to maintain the condenser pressure as constant as possible.
Air Circuit
- Air inlet Hot saturated air enters the dryer and is cooled by the outgoing air via the air-to-air heat exchanger. Reducing the temperature of the inlet air reduces the load on the refrigerant circuit(FX5 and above only)
- Air outlet Re-heats the outgoing air to prevent condensation on the factory's pipe work(FX5 and above only)
- Air-to-refrigerant heat exchanger Transfers heat from the compressed air to the cold refrigerant, forcing water vapour in the compressed air to condense. The more effective the heat transfer, the cooler the air becomes and the more water vapour condenses.
- Water separator Collects and drains off condensate from the cooled air flow. The more efficient the separation, the better the pressure dew point, as droplets which are not collected revapourise and degrade the pressure dewpoint.
- Air-to-air heat exchanger All models include an air-to-air heat exchanger as standard, which prevents condensation forming on the outside of the pipe system.
Features
Solid Performance
- Steady pressure dew point
- No freezing of condensed moisture
- No chance of moisture entering the compressed air system
Easy installation
- Plug and play concept
- Single electrical connection
- All units pre-commisioned
- Self regulating
Significant cost saving
- Increased reliability and lifetime of tools and equipment
- Reduced pipe work leaks, meaning reduced energy bill
- Fewer repairs to tools, machines and pipework
- Less inconvenient breakdowns and stoppages
- Minimal chance of product spoilage through moisture carryover
Simple reliability
- Quality components, generously sized
- Simple and proven design
- Effective control system (hot gas bypass)
Minimal maintenance
- Long service intervals
- Few component replacements
- Ergonomic design for fast access to key components
Environment friendly
- Compliant to strictest environment regulations
- CFC free refrigerants
As a matter of fact, a pressure dew point lower than the ambient temperature will avoid condensation in the compressed air system. But this is not enough to prevent corrosion. Depending on the pipe material, corrosion may start if the relative humidity in the air net is above 50% Based on these facts, a relation between the ambient temperature and the pressure dew point required to avoid corrosion can be established. The area below the dotted line represents a relative humidity lower than 50%, for example, for an ambient temperature of 25 C a pressure dew point of 13 C or lower is enough to prevent corrosion Correspondingly it is sufficient to maintain a pressure dew point below 28 C at an ambient temperature of 40oC to prevent air net corrosion. As a thumb rule a dryer providing a pressure dew point 12 C below the ambient temperature will avoid water in the compressed air system and will protect the airnet against corrosion.